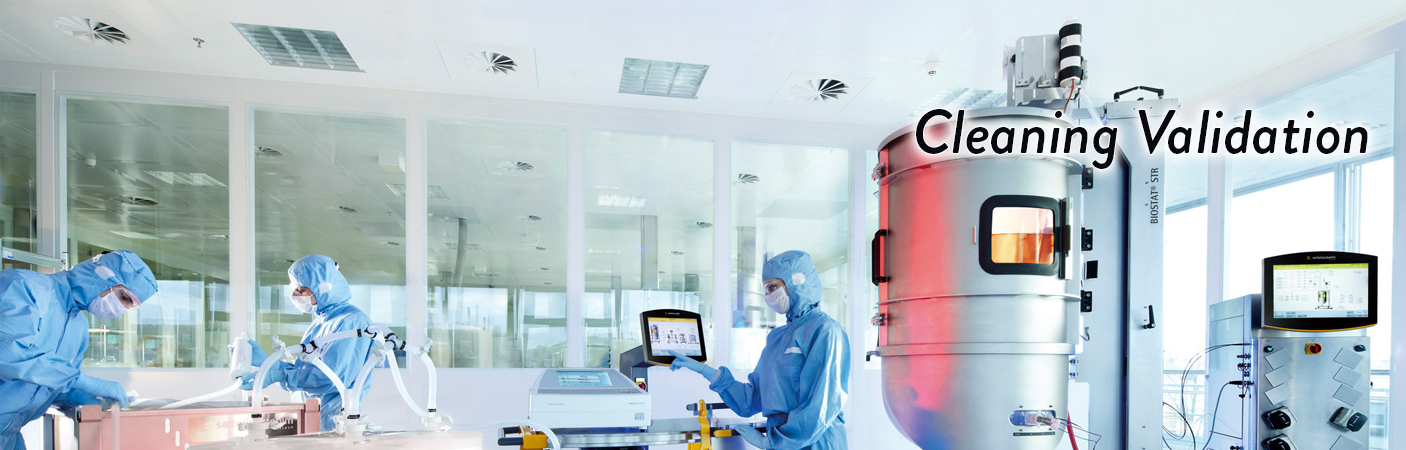
Cleaning Validation is the Methodology used to assure that a Cleaning Process removes Residues of the Active Pharmaceutical Ingredients (APIs) of the Product Manufactured 1in [on] a piece of equipment, the cleaning Aids utilized in the Cleaning Process, and the Microbial attributes to ensure that the process and processing Equipment are suitable 2for [subsequent] Pharmaceutical Manufacturing. Potential Contaminants include Residues of the APIs, API Degradation Species, or Residues from the Cleaning Process such as Detergents or Solvents.
All Residues are removed to Predetermined levels3 to ensure the Quality of the Next Product Manufactured is not compromised by Waste from the previous Product and the Quality of future Products using the Equipment, to prevent Cross-Contamination and as a GMP Requirement.
[levels so as to ensure that the Quality of Product to be Manufactured next on the Equipment, is not compromised by Waste from the previous product, to prevent Cross-Contamination and as a GMP Requirement]
Acceptable Residue Limits (ARL) in Cleaning Validation is a Critical function and should be Practically Achievable, Verifiable for Logical Determination. This covers the Critical 10 ppm USP Limit Test on Materials for which no Toxicology Data is available.
Validation of Cleaning Procedures is not normally required but a Risk Assessment should be performed to make sure that there is no potential for Degradation or Microbial Contamination that may adversely impact the Quality of the Product. The Analytical Methods for Cleaning Validation should be Validated & Suitable to Quantify at the Acceptance Criterion Level. The Limit of Detection (LOD) must be lower than or equal to the Acceptance Criterion Level. Blanks must be evaluated to ensure that there is no significant interference with4 [from] the Recovery of the Analyte.
EFRAC’s Cleaning Validation services include Validation of Cleaning Procedures, Challenge Tests for Equipment Cleaning Process & Equipment specific Sampling through Visual inspection, Swab sampling or Rinse Sampling, Limit Test 5or cover a range of Analyte Concentration [and cover a range of Analyte Concentrations.] The broad Cleaning Validation Sampling Techniques cover Swabbing, Rinsing & other appropriate or Specific Techniques.
Cleaning Validation
• Organic Ingredient Residue
• Inorganic Ingredient Residue
• Microbial Contaminants
• Toxic Organic Volatile Impurity [Volatile Organic Impurity]
• AAS (Flame, GTA, VGA) • ICP-MS • ICP-OES • FT-IR • LC-MS-MS (QQQ) • GC- (FID, HEAD SPACE, ECD, MS) • GC-MS-MS (QQQ) • HPLC (FLD,PDA ,ELSD,RID) • IC–CD/AD/UV • Karl-Fisher Autotitrator Potentiometer • Refrigerated Centrifuge • Rota Evaporator • TOC Analyzer • UV–Visible Spectrophotometer • RT-PCR • ELISA Reader
• British Pharmacopeia [Pharmacopoeia]
• European Pharmacopeia [Pharmacopoeia]
• Indian Pharmacopeia [Pharmacopoeia]
• Japanese Pharmacopeia [Pharmacopoeia]
• United States Pharmacopeia [Pharmacopoeia]